There are several methods used in aluminum manufacturing. Two prominent techniques include die casting and extrusion. Die casting uses a high-pressure injection of molten aluminum into steel molds, allowing complex internal shapes to form. Extrusion pushes heated aluminum through shaped dies to continuously produce cross-sectional profiles. While utilizing varied technical approaches that impact component attributes, both aluminum die casting and aluminum extrusion are mainstay processes within the industry. They are critically important in aluminum fabrication.
Understanding Aluminum Die Casting and Extrusion
Aluminum die casting involves first melting aluminum using intense heat. This rendering process produces a liquid metal formulation. Next, the molten aluminum mixture is forced into a steel mold-shaped cavity at intense pressure. The high pressure fills the die details and solidifies the part near-instantaneously. Die casting produces complex items with fine surface finishes and integrated features. Automotive components and electronics housings are common applications.
The aluminum extrusion process involves heating aluminum billets or rounds to high temperatures and passing the malleable aluminum through a steel die opening. As it passes through, the material assumes the desired shape profile of the final product. Extruded parts may have intricate hollow sections, channels, and multiple walls. Key aluminum forming applications include construction beams, pipes, and vehicle doors or frames.
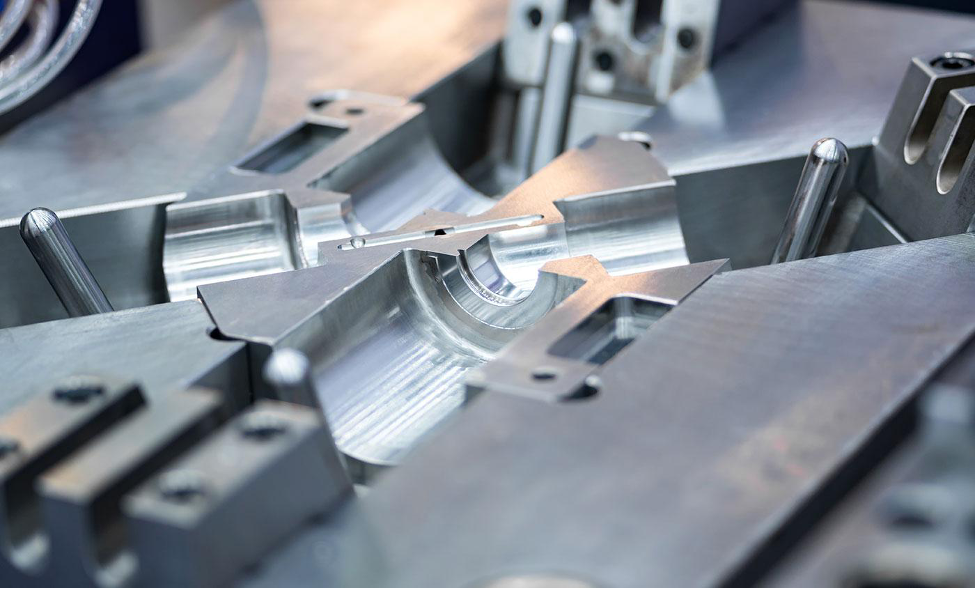
Key Differences Between Aluminum Die Casting and Extrusion
While die casting and extrusion yield quality aluminum parts, their process variation leads to differences in the resulting product attributes and applicable industries:
1. Process Variation
Aluminum die casting sees molten aluminum injected forcefully into reusable molds under intensive pressure. This allows internal geometries to set quickly into precise near-net shapes. Comparatively, aluminum extrusion heats aluminum profile stock and pushes it continuously through pre-formed openings, enabling indefinite cross-sectional profiles with consistent dimensions.
2. Product Characteristics
The fast solidification within die-casting molds results in finely detailed parts with integrated features and complex hollow chambers. Extruded products emerge as solid or hollow profiles that can span limitless lengths. Transportation of molten aluminum also induces porosity risks in die casts, whereas extruded items exhibit homogeneous microstructures.
3. Applications and Industries
Because of form flexibility and repeatability, die-cast aluminum is suitable for electronic gadgets, small appliances, and automotive trim. Aluminum extrusion, on the other hand, caters mainly to construction, transportation, and industrial equipment manufacturing through its continuous profile productivity.
Comparative Analysis
Evaluating key differences through a comparative study is important to determine the most suitable fabrication process. A deeper analysis of strengths, limitations, costs, and efficiencies provides valuable insights:
1. Strengths and Limitations
Die casting excels in producing intricate near-net shape components with tight tolerances and embedded inserts. However, design changes may require the replacement of expensive tooling. Extrusion allows the formation of endless profile lengths easily, but intricate internal features or geometry modifications incur high costs.
2. Cost and Efficiency
Initial tooling costs for die-casting molds are substantial, but the costs drop with increasing part volumes. Setup expenses for low-volume aluminum extrusion runs are higher due to heating/conditioning needs. However, extrusion tooling expenses are minimal, making it very cost-efficient for long production runs. Material yield rates are higher for extrusion as compared to some material waste in die-casting sprues and runners.
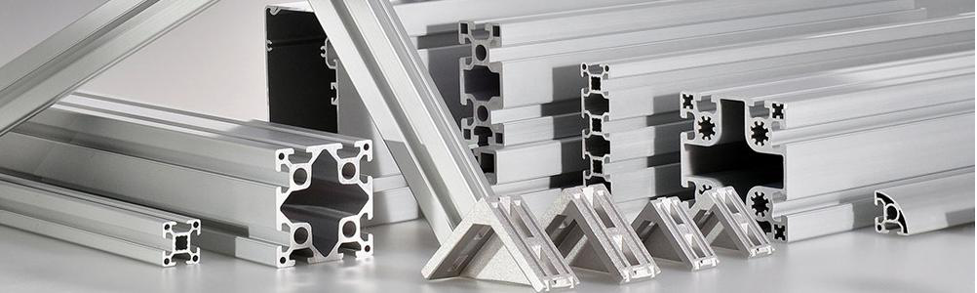
HordRT Offers Both Aluminum Extrusion and Aluminum Die Casting Services
HordRT is a leading custom manufacturer that offers reliable aluminum extrusion, die casting, and prototyping services. The company has streamlined production capabilities to deliver high-quality customized parts at competitive costs. Backed by reliable suppliers and strict quality control, the brand has gained a strong reputation among customers for its expertise, quick turnarounds, and exceptional after-sales support catering to various industries globally.
HordRT offers precise aluminum die casting through pressure injection. With expertise in this field, the service provider casts intricate parts in common alloys such as A356 and A380. Automotive components, electronics housings, and more are manufactured. Optional post-casting processes include anodizing and powder coating to enhance surfaces.
HordRT’s aluminum extrusion services utilize alloys 6061 and 6063 that are known for strength, corrosion resistance, and extrudability. Profiles are made in hollow or solid profiles of any length for construction, vehicles, and more. The company delivers quick turnarounds with standard finishes or customized surfaces like polishing and painting. Prototypes and low-volume production are available to customers through the brand’s relationships and production abilities.
Conclusion
Aluminum die casting and extrusion are distinct manufacturing processes, each with unique strengths and applications. Die casting excels in intricate, detailed parts for electronics and automotive uses, while extrusion offers limitless profile lengths for construction and industrial sectors. Choosing between them depends on factors like design complexity, production volume, and cost efficiency. Proficient in both techniques, HordRT provides tailored, high-quality parts efficiently, meeting diverse industry needs with precision and reliability. You can contact HordRT to learn more about its aluminum fabrication and tooling services.