Extrusion processes form parts by pushing hot metal or thermoplastic material through a die to create a continuous profile. Aluminum & plastic extrusion is particularly popular and widely used because it facilitates complex profiles that are otherwise challenging or impossible to achieve through alternative methods. Its importance is evident in an extensive array of industries for crafting both structural and functional components.
Understanding Aluminum Extrusion
In the process of aluminum extrusion, the material is brought to its elevated working temperature and situated within the vessel or billet feed chamber of an extrusion press or container. As the aluminum is pushed out under heavy pressure, it flows smoothly through a steel die profile. This imparts the desired cross-sectional shape to the material as it emerges from the die outlet.
Aluminum extrusion offers excellent mechanical properties, versatility across industries, strength compared to other metals like steel, and corrosion resistance. Its light weight also makes it energy efficient to transport finished goods. It finds applications in construction, transportation, electronics enclosures, and solar panel frames.
Insights into Plastic Extrusion
In plastic extrusion, the material in pellet or granular form is fed into a heated barrel. As it is pushed through, rotating screws apply intense pressure and heat the plastic mass above its melting point. The melted plastic then flows through a die opening, shaping it into the desired cross-section.
Plastic extrusion offers flexibility to produce endless variants from a single die with quick color changes. It also enables dimensional accuracies, surface finishes, and crisp details depending on the die design. The process is highly cost-effective for mass-producing consistent plastic parts and components.
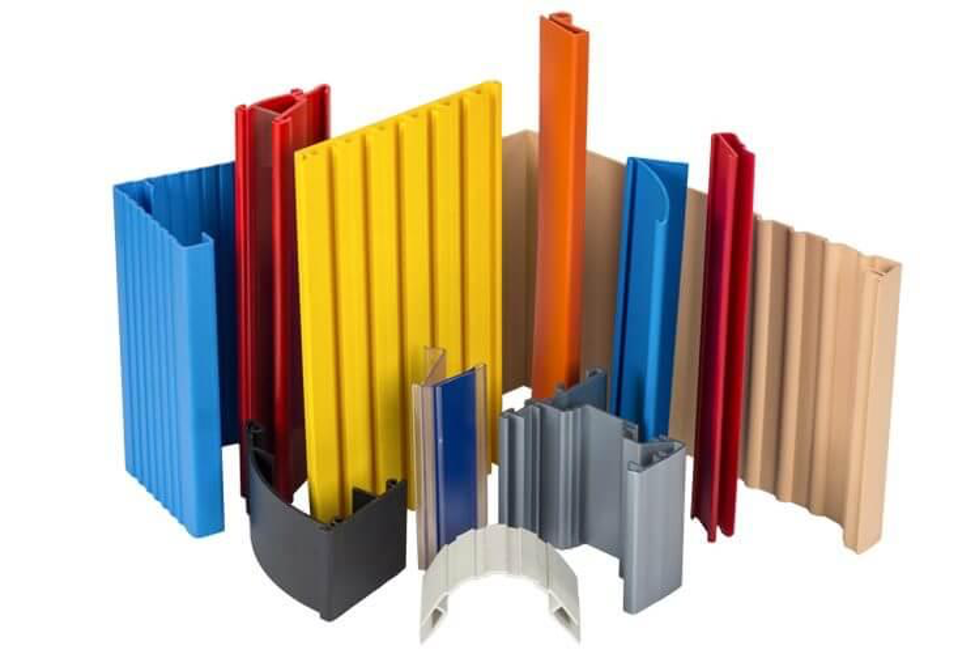
Contrasting Aluminum and Plastic Extrusion
Understanding the fundamental distinctions between aluminum and plastic extrusion begins with a closer look at their respective materials and preferred applications.
1. Materials
Aluminum extrusion relies on alloys such as 6063 or 6061, chosen for their corrosion resistance and durability, particularly in demanding environments. These alloys provide structural integrity and strength, making die-cast aluminum a favored choice for applications requiring robust materials. On the other hand, plastic extrusion primarily utilizes thermoplastics like PVC, PE, PP, and PS. These materials possess malleability when heated, allowing for easy shaping and molding into various forms.
2. Applications
Aluminum extrusion finds its niche in industries like construction, transportation, and machinery due to its inherent rigidity and strength properties. Its utilization in these sectors ensures structural stability, making it a preferred choice for components that demand durability. Conversely, plastics dominate industries such as consumer goods, packaging, piping, and medical applications. Their affordability and versatility make them well-suited for applications where cost-effectiveness and adaptability to diverse shapes and forms are crucial.
Choosing the Right Extrusion Process
Some critical factors that influence the choice between aluminum & plastic extrusion include:
1. Strength
Aluminum’s standout feature lies in its exceptional strength-to-weight ratio, which is ideal for load-bearing structural parts. In contrast, plastics offer moderate strength suited for non-load applications and cosmetic purposes, providing versatility in various scenarios where robust strength isn’t the primary requirement.
2. Cost Considerations
Aluminum typically incurs higher initial tooling costs compared to plastics, especially in thermoplastic processing, which involves lower setup expenses. However, for higher production volumes, custom plastic extrusion may present lower upfront and per-unit costs. Despite this, the long-term sustainability and recyclability benefits of aluminum offset its initial expenses, making it a viable, eco-friendly choice in the extended lifecycle of the material.
3. Surface Finish Options
Aluminum yields sleek, polished surfaces, rendering it a preferred choice for premium aesthetics. Conversely, plastics offer a wider spectrum of finishes, ranging from glossy to textured, achieved through diverse tooling techniques. While polished aluminum adds sophistication, the diverse tactile finishes of plastics cater to varying design preferences and aesthetics.
4. Design Flexibility and Adaptability
Plastics excels in design flexibility, offering unlimited color changes and rapid modifications to designs and tooling. This stands in contrast to aluminum, which requires more time and cost for customization due to limitations in altering crafted tooling. The adaptability and ease of alterations provided by plastics make them advantageous in scenarios requiring frequent design changes or diverse aesthetic requirements.
The comparison between aluminum and plastic extrusion methods serves as a guide for selecting the most suitable process based on critical considerations like strength requirements, cost implications, desired surface finishes, and the level of design flexibility needed for the intended applications.
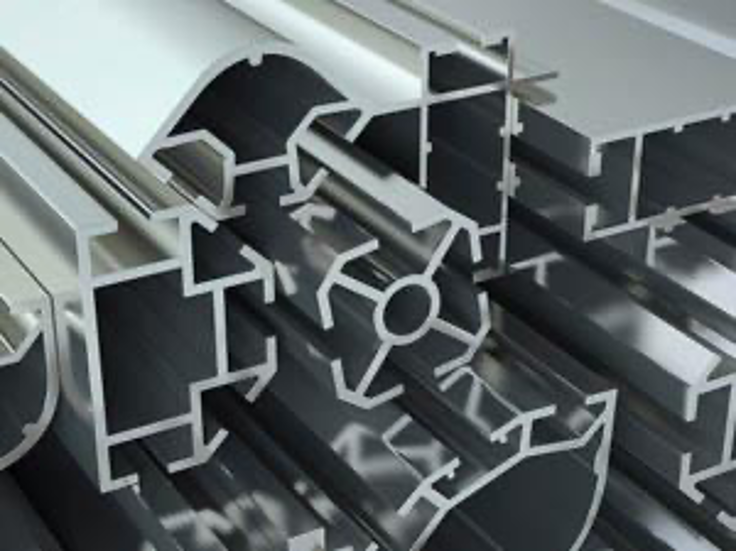
HPrapid’s Aluminum & Plastic Extrusion Service
HPrapid specializes in rapid prototyping, CNC machining, customized aluminum and plastic extrusion, aluminum forming, and other manufacturing services. The company is well known for employing cutting-edge equipment, stringent quality control processes, and material verification approaches. Its dependable aluminum & plastic extrusion and custom manufacturing services provide customers with complex profiles and parts within quick turnaround times.
HPrapid offers aluminum & plastic extrusion that transforms raw materials into specified cross-sectional profiles for plastic or aluminum materials. The company efficiently handles projects of all sizes. Key benefits include partners for short-run custom extrusion extrusions with excellent quality and lead times. In-house CNC machining enables precise post-processing. Design consultations aid in functionally shaping plastics/alloys through prototyping to medium production. The manufacturer provides a streamlined solution to customers, from concept development through bulk order fulfillment. With its expertise and resources, you can have peace of mind that your custom extrusion projects are in capable hands.
Conclusion
The choice between aluminum and plastic extrusion boils down to this: aluminum for strength and durability in construction and transportation, plastic for versatility and cost-effectiveness in consumer goods and medical applications. Factors like strength, cost, finish options, and design flexibility guide the decision. Companies like HPrapid offer tailored solutions, using advanced tech to meet specific needs within tight deadlines and quality benchmarks. Reach out to HPrapid on its website for reliable, cost-effective aluminum & plastic extrusion services for all your project needs.