Working in the manufacturing sector, you must understand that enhanced customer satisfaction is of paramount importance. This is why getting ISO 9001 certification can help you achieve the next level of business success. Let us discuss how ISO 9001 can help manufacturing organisations succeed.
What do manufacturing organisations require to succeed?
Let us keep ISO 9001 standard aside for a moment and discuss the core needs of manufacturing organisations. Although every business has different requirements, specific basic needs must be fulfilled to achieve success. For example, every business requires a defined process that is constantly reviewed to find areas of improvement. This is because enhanced efficiency of processes cannot only help organisations achieve cost controls but can also help mitigate any potential risks.
Similarly, businesses also require a specific set of standards that can be utilised to define characteristics of an “acceptable” product or service. Without such specifications, manufacturing companies cannot distinguish between an underperforming or substantial product a one that their customer will love. Moreover, in addition to having a defined process and specific standards, you need knowledgeable staff and the resources to produce a high-quality product or service.
Now, let us talk about what the management needs to do to appropriately utilise these resources. The management requires better insight and higher transparency so that any inherent flaws can be found. This means that the management needs to conduct audits to review processes, collect feedback from the customer and implement corrective actions to ensure that problems are fixed in a satisfactory manner. If done properly, applying corrective actions also ensures that these issues do not return.
Based on what is written above, we can conclude that a systematic framework is required to consistently produce a service or a product of a specific quality. So, how does ISO 9001:2015 helps us in creating this consistency?

How can ISO 9001 help you succeed?
As mentioned above, to create consistent product/service quality, we need defined processes, standards, competent staff and managerial insight. ISO 9001 can help you succeed by:
- Creating defined processes: The various clauses in the standard, such as performance evaluation, operation, support or planning, help you define the context of the organisation, allowing your company to ensure that all the essential factors and obligations have been considered. This will allow you to define your processes accurately and appropriately.
- Set of specific standards: Clause 8 of ISO 9001 outlines the requirements of products or services and, under the heading operation, delineates the requirements that allow companies to accurately define the specifications regarding their products and services.
- Knowledgeable staff: A crucial part of ISO 9001 is supported in clause 7, which includes competence, awareness, organisational knowledge, and people. If business owners adhere to this clause, they will enhance their staff’s competency, knowledge base and awareness regarding quality management.
- Better managerial insight: In section 9 of the standard, entitled performance evaluation, there are many recommendations for reviewing and measuring that help managers create a sort of “tollgate” on the product characteristics and quality. Similarly, section 10.2 deals with non-conformities and corrective actions, and adhering to this section will help managers correct an incident and display the tactics that prevent its reoccurrence.
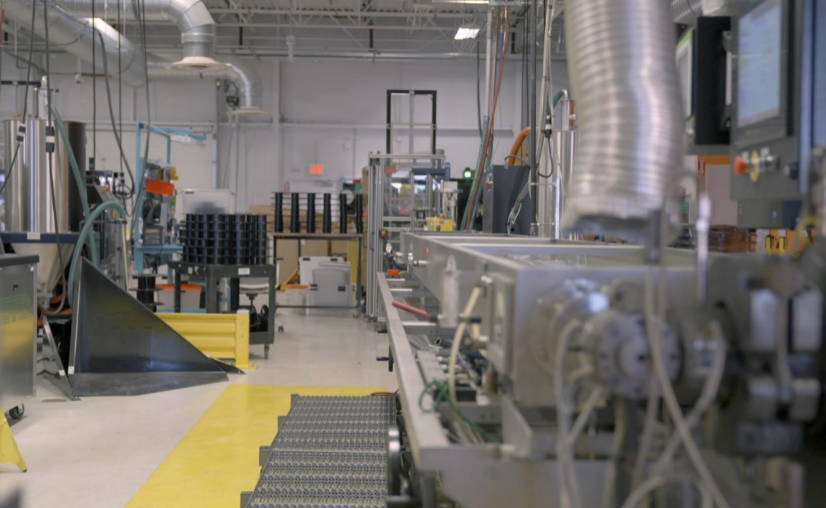
ISO 9001:2015 in manufacturing
In addition to defining your processes, creating a specific set of standards, increasing the knowledge of your staff and enhancing managerial insight, there are many more benefits of ISO 9001 for your factory. The benefits of the Plan Do Check Act (PDCA) cycle are obvious, helping manufacturing organisations review the efficiency of the processes in a systematic manner. With the help of internal audit and management reviews, product intelligence can be increased in manufacturing organisations, as the managers and leaders can appropriately plan before action, review, correct, and modify the quality of the product as per their customer requirements.
However, getting ISO 9001 certified also helps solidify your position as an industry leader, as the certificate is considered lucrative and prestigious. Now, not only will your stakeholders have more confidence in your ability to consistently produce high-quality goods, but customers who were hesitant to buy from you before will happily purchase your products. This is because you will be able to understand the exact needs of your target audience and modify your products to suit their taste. When a product is functional, reliable, safe, efficient, and high-quality, there is nothing that will stop a customer from re-purchasing it. ISO 9001 will push you to the next level of business success.
ISO 9001 consultant
Implementing a Quality Management System (QMS) is much more than just reading the clauses. Business owners must understand the context of the organisation, identify the expectations of the interested parties, ensure that they adhere to all legal obligations, conduct a gap analysis to find deficiencies, align the documents and train their staff. An ISO 9001 consultant simplifies the process, refining your QMS to keep improving as time progresses.
Conclusion
ISO 9001 gives manufacturing organisations precisely what they need to succeed and grow their business, including defined processes, specific standards, knowledgeable staff, and better managerial insight.