PCTG and PETG are commonly used thermoplastics in injection molding. Both maintain clarity and withstand manufacturing processes like injection molding. However, selecting the right material depends on the part’s intended use and required properties. The choice of PCTG versus PETG for injection molded components can impact various key characteristics. These include transparency, strength, flexibility, and operating temperatures. Comparing helps decide which performs best for a plastic component’s intended use.
Understanding the Materials
Both PCTG and PETG offer desirable properties for injection molding but vary in specific characteristics.
1. Definition and Composition
PCTG is a thermoplastic with a cycloaliphatic structure. It features cyclohexanedimethanol(CHDM), terephthalic acid, and polyethylene glycol. These elements provide the rigid cyclohexane backbone structure.
PETG is a thermoplastic polyester. The ethylene glycol component is modified; it is either replaced with or blended with cyclohexanedimethanol or other additives. This element enhances the flexibility of PETG.
2. Key Properties and Characteristics
PCTG exhibits good clarity and high heat resistance up to 150-180°C[1]. It is also more chemically resistant. However, it has a lower impact strength than PETG. PETG is more flexible; it absorbs impacts nicely without breaking. While its heat deflection is lower around 80-85°C[1], it maintains clarity well and resists chemicals commonly.
3. Typical Applications and Industries
PCTG finds use in applications that need durability. This includes medical devices or electrical/automotive parts. Its clarity, heat tolerance, and chemical resistance make it suitable. PETG is commonly used in consumer products and packaging. Its flexibility allows it to withstand minor impacts better.
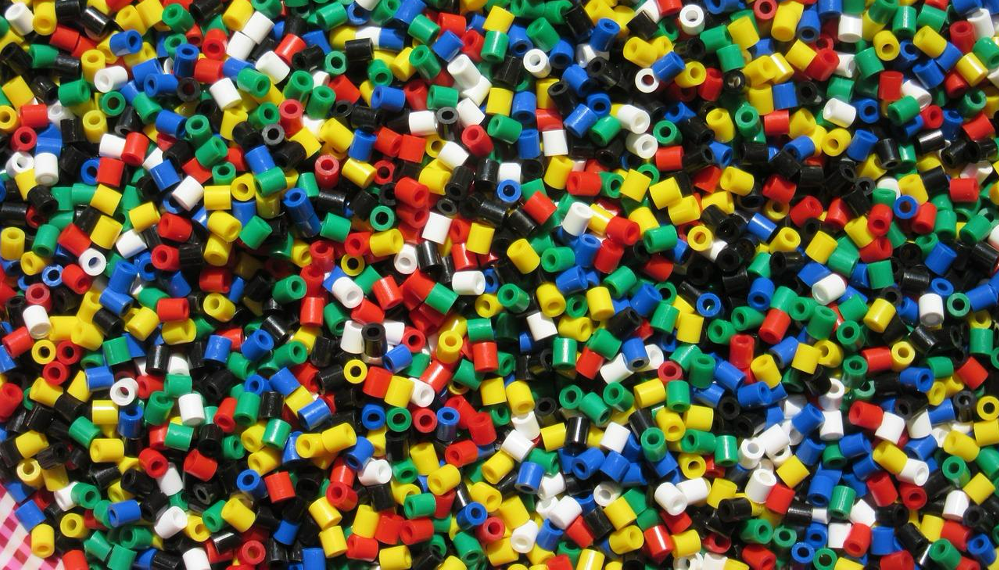
PCTG vs PETG – A Side-by-Side Comparison
Comparing the qualities of these materials is valuable. It aids in deciding which performs best for a given injection molded part.
1. Comparative Analysis of Properties
The following properties and aspects highlight the difference between PCTG and PETG:
A. Transparency
Both PCTG and PETG maintain transparency. However, they differ in retaining clarity over time. PCTG exhibits excellent transparency. When exposed to UV light, the transparency is retained long-term. PETG also remains transparent initially; however, it may develop a slight yellow tint when exposed to UV over an extended period.
B. Impact Resistance
Where withstanding impacts is important, PETG has an advantage over PCTG. It absorbs higher impacts without breaking compared to the more brittle PCTG. This makes PETG better suited for reusable containers or applications that involve minor bumps or stresses.
C. Heat Resistance
PCTG can withstand temperatures of up to 150-180°C, which gives it an edge over PETG for applications near heat sources or involving hot liquid handling. On the other hand, PETG maintains its integrity only up to around 80-85°C depending on specific additives used. PCTG also exhibits better dimensional stability at higher operating temperatures.
2. Environmental Impact and Sustainability Considerations
Recyclable PET is the base material of both types, producing less waste than alternatives during manufacturing. PCTG manufacturing requires less energy usage compared to PETG and releases fewer volatile organic compounds. However, PETG may offer slight advantages through its enhanced flexibility. It potentially reduces material needs for some applications. Overall, both options provide viable eco-friendly solutions.
3. Cost Comparison
The cost incurred depends on volume and tooling needs. Overall, PCTG production incurs higher costs than PETG. It’s because of the additional processing steps for the more complex chemistry involved. However, PCTG’s improved properties may justify the larger per-unit price for certain applications. These include those where characteristics like heat tolerance, transparency, or chemical resistance take priority.
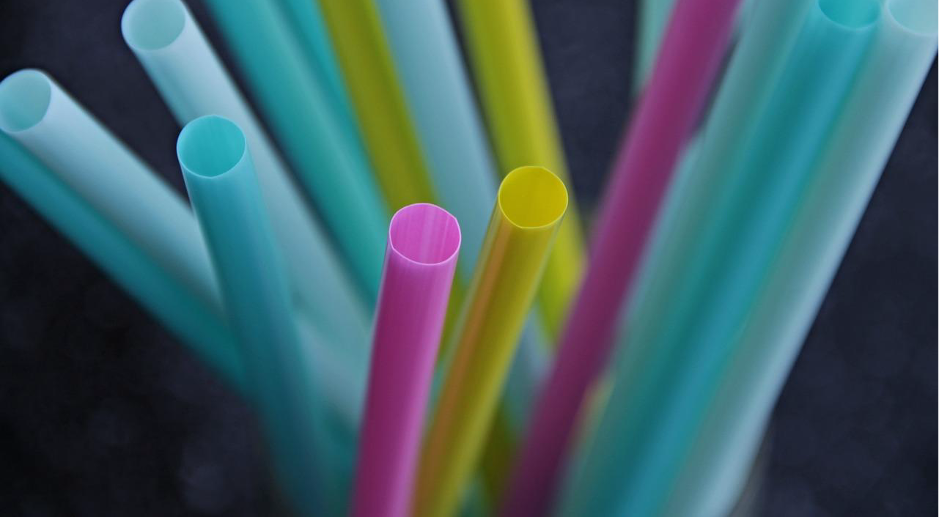
Injection Molding Services from HordRT
HordRT is a leading provider of plastic injection molding solutions. Over the years, the company has grown to become an experienced manufacturing partner. Plastic injection molding is one of the brand’s core services. HordRT handles projects of all complexities and sizes with this service. Parts are produced using a variety of industrial-grade thermoplastics. The key advantages include:
- High-quality injection molded parts within targeted timelines
- Professional design for manufacturability analysis and optimization
- Production lead times as short as 10-15 days
- Diverse selection of injection molding materials and surface finishes
- Cost-effective solution from prototype to tens of thousands of units
- No minimum order quantities required
- Rapid prototyping that accelerates product development
Conclusion
Overall, both PCTG and PETG have advantages depending on the injection molded part’s intended use. When clarity, heat resistance, or chemical tolerance prove critical, PCTG offers an edge. However, PETG delivers better impact strength and flexibility benefits. It’s more suited to reusable containers or flexible packaging. The reputed brand HordRT offers reliable injection molding services. It works diligently to understand clients’ needs to determine which plastic meets the requirements for molded components. Visit the company’s website to explore its full line of prototyping and production solutions.
References
[1] PCTG filaments: Everything you need to know. Available at: https://azurefilm.com/2023/10/12/pctg-filaments-everything-you-need-to-know/ (Accessed: 16th, August)